Large-area Photogrammetry Based Testing of Wind Turbine Blades
Document Type
Article
Publication Date
3-1-2017
Publication Title
Mechanical Systems and Signal Processing
Abstract
An optically based sensing system that can measure the displacement and strain over essentially the entire area of a utility-scale blade leads to a measurement system that can significantly reduce the time and cost associated with traditional instrumentation. This paper evaluates the performance of conventional three dimensional digital image correlation (3D DIC) and three dimensional point tracking (3DPT) approaches over the surface of wind turbine blades and proposes a multi-camera measurement system using dynamic spatial data stitching. The potential advantages for the proposed approach include: (1) full-field measurement distributed over a very large area, (2) the elimination of time-consuming wiring and expensive sensors, and (3) the need for large-channel data acquisition systems. There are several challenges associated with extending the capability of a standard 3D DIC system to measure entire surface of utility scale blades to extract distributed strain, deflection, and modal parameters. This paper only tries to address some of the difficulties including: (1) assessing the accuracy of the 3D DIC system to measure full-field distributed strain and displacement over the large area, (2) understanding the geometrical constraints associated with a wind turbine testing facility (e.g. lighting, working distance, and speckle pattern size), (3) evaluating the performance of the dynamic stitching method to combine two different fields of view by extracting modal parameters from aligned point clouds, and (4) determining the feasibility of employing an output-only system identification to estimate modal parameters of a utility scale wind turbine blade from optically measured data. Within the current work, the results of an optical measurement (one stereo-vision system) performed on a large area over a 50-m utility-scale blade subjected to quasi-static and cyclic loading are presented. The blade certification and testing is typically performed using International Electro-Technical Commission standard (IEC 61400-23). For static tests, the blade is pulled in either flap-wise or edge-wise directions to measure deflection or distributed strain at a few limited locations of a large-sized blade. Additionally, the paper explores the error associated with using a multi-camera system (two stereo-vision systems) in measuring 3D displacement and extracting structural dynamic parameters on a mock set up emulating a utility-scale wind turbine blade. The results obtained in this paper reveal that the multi-camera measurement system has the potential to identify the dynamic characteristics of a very large structure.
Volume
86
Issue
B
First Page
98
Last Page
115
DOI
https://doi.org/10.1016/j.ymssp.2016.07.021
ISSN
0888-3270
Rights
© 2016 Elsevier Ltd.
Recommended Citation
Poozesh, Peyman; Baqersad, Javad; Niezrecki, Christopher; Avitabile, Peter; Harvey, Eric; and Yarala, Rahul, "Large-area Photogrammetry Based Testing of Wind Turbine Blades" (2017). Mechanical Engineering Publications. 117.
https://digitalcommons.kettering.edu/mech_eng_facultypubs/117
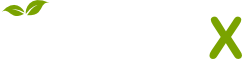
- Citations
- Citation Indexes: 160
- Patent Family Citations: 1
- Usage
- Abstract Views: 11
- Captures
- Readers: 127
Comments
ESSN: 1096-1216